Earlier in my profession, I was a commercial upkeep manager. I had the benefit of leading a world-class maintenance company at one center as well as starting a system up from scratch at one more (as well as a couple of that remained in between). I remained in the Navy Nuclear Power Program so I have a respectable concept of what great upkeep is.
Power Efficiency requires to be a vital part of the upkeep collection yet regrettably rarely is that ever before the case. Upkeep specialists can conveniently comprehend the technical and also company ramifications of energy performance however they are usually not part of the conversation. That needs to transform, due to the fact that no team can influence power effectiveness (both great as well as bad) as high as the maintenance department can.
What takes place when maintenance is not part of the discussion? Here are a few instances:
A new Energy Management System is mounted. After a few months, no obvious reduction in energy usage has actually occurred. Examination reveals the majority of the system has been jumpered out by the upkeep department. The reason for this is that maintenance got no training on the system as well as its advantages. Maintenance still needed to make customers delighted and also uneasy with the automation, so they went back to the hands-on system they understood. This can happen for several years if no person is keeping track of the systems.
Reduced effectiveness electric motors are repaired instead of changed when failings occur.
V grooves as opposed to scratched belts are made use of simply because “they were in supply”Equipment that falls short is replaced with the precise same equipment, without any idea of more recent modern technology requirements was composed 2 decades ago, yet it still must be excellent, appropriate?
This is my personal fave. Devices are left running 24/7 due to the fact that there is the worry that if it is shut off it will certainly not turn back on.
However, this frame of mind enters into play often on the largest of lots such as chillers, pumps, central heating boilers, and so on. In big manufacturing facilities, the issue can be a lot even worse. I recall the use of compressed air “blow-offs’ to keep insects from jumping on the product. It was a seasonal concern that beetles would unavoidably jump on the product sheet (galvanized steel), get crushed as the sheet undergoes the process line, and create quality issues. This “blow-off” was primarily a pipeline with openings pierced into it.
Given that a 1/4″ hole at 100 psi expenses concerning $10,000 a year in energy, one can simply think of the cost of running this gadget 24/7 for months at a time. Since power use and also expense was designated to a different department and also the end-user was never ever part of the loophole, these circumstances are inescapable.
So what can be done? Below are a few ideas that would most definitely be a good beginning.
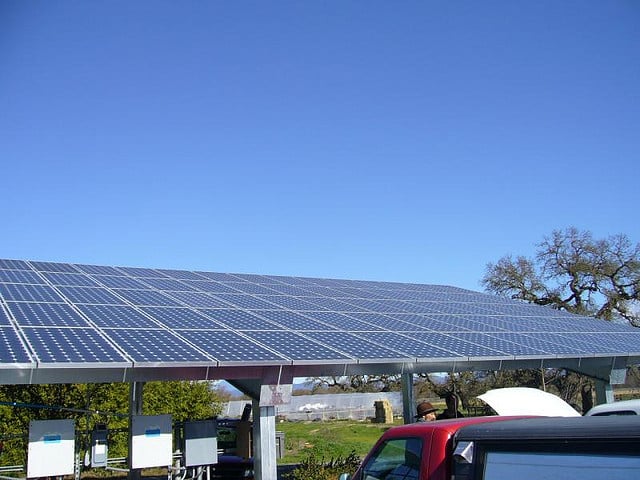
Train, train, train!
Yes, I recognize that you believe when you hire these people they ought to currently understand whatever, however, points adjustment. Tribal expertise (word of mouth or the old “stay with so and so for a while until you recognize what you are doing”) just is not a regular technique as well as occasionally poisonous substances the whole division due to the fact that the “go-to-guy” might not be the best instructor (or may have some bad habits). Visit AZ Big Media where you will find lots of great information and practical advice about energy use.
Sharing real-world examples of exactly how maintenance impacts power usage can go a long way in obtaining buy-in from the maintenance division. There is typically an energy cost connected with choices that the maintenance department makes. There are situations, at times when management and assistance personnel are not available, that the on-site upkeep personnel has to buy authority. By being informed pertaining to energy effectiveness, they can make the best service decision and also protect it.
A good example would certainly be a simple a/c electric motor. Upkeep service technicians need to know about the much greater long-lasting costs related to buying the cheapest possible electric motor. Knowing that the first cost of an electric motor is just 5% of its overall operating cost, absolutely aids in making the ideal decision. Understanding the annual prices connected with operating motors needs to demonstrate how vital it is to close them off when they are not needed.
Vendors commonly will train for free. I discovered that drive belts provide an outstanding training opportunity. The supplier will certainly reveal to specialists the appropriate means to install and stress a belt, and also the advantages/disadvantages of the different sorts of belts. It is unbelievable that you will still see skilled maintenance professionals utilize a screwdriver or crowbar and “stretch” a belt over a sheave. This is a big no-no and also is bad for the belt. This was probably found out by “tribal expertise”!